Machine Downtime Tracking: Short-Term Savings Turns Into Long-Term Gains
- downtimecollection
- Sep 13, 2023
- 2 min read
When manufacturing businesses begin to experiment with equipment downtime tracking, they normally do so with an eye towards the short-term benefits they're promised by solutions providers. They're dealing with frustrating and costly unplanned downtime, and they need it to stop as quickly as possible.
For many, the most obvious benefit of equipment downtime tracking has to do with the cost savings you begin to enjoy almost immediately. If you can stop a critical piece of machinery going down unexpectedly for even a half hour, that's 30 minutes more in a day when you can generate revenue. That's 30 minutes extra where your workers are operating at peak efficiency, and when you don't have to worry about finding (and buying) things like replacement parts.
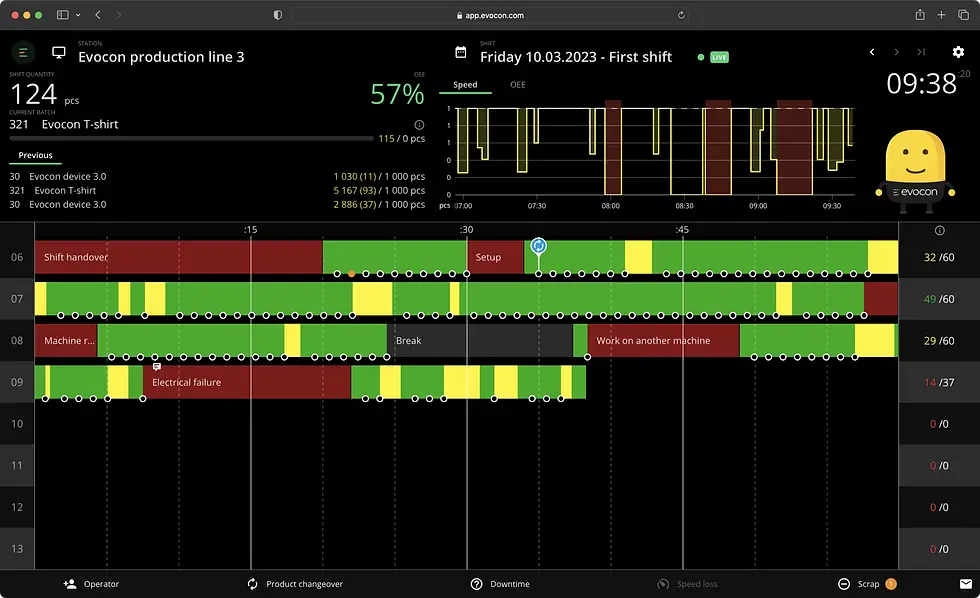
But while this is important, it's also only the beginning of something far better: continuous improvement across your entire business.
Tracking Machine Downtime: Playing the Long Game
It's a good thing that a machine downtime tracking solution is warning you in advance when conditions are deviating from the accepted definition of "normal," all so that you can stop a small problem today before it has a chance to become a bigger one later on. These solutions are also designed to help fend of those costly repeat issues that seem to rear their ugly heads at the worst possible moment.
But as you collect and analyze more data, you also understand why those problems are occurring in the first place. You stop treating the symptom and start treating the disease, so to speak.
Over time, your maintenance processes begin to improve organically. Whether you're dealing with a question of inadequate employee training or a lack of resources or ineffective maintenance or something else entirely, these concerns start to go away as you have more insight into their nature. At that point, you don't have to worry about avoiding those downtime-related problems because you're starting to see fewer and fewer of them to begin with.
This has a positive ripple effect in other ways, too. As you learn more about what works for your business, you can create new standard operating procedures that make sense given your unique environment. Your preventative maintenance programs naturally become more effective, but it also becomes easier to train new employees whenever you bring them into the fold. You can train new workers not in a general way, but in terms of precisely what they need to know to get the job done and keep things up and running.
This again translates into an enormous cost savings because people can immediately be at their best as soon as they hit the floor. All these are benefits that would be difficult to enjoy without machine downtime tracking at your side.
If you'd like to find out more information about why it's always important to focus on the long-term gains of machine downtime tracking, or if you'd just like to speak to someone in more detail about what a solution like Thrive can do for you, please don't delay - contact us today.
Comments