What "Digital Twins" Mean for Machine Downtime Tracking
- downtimecollection
- Jul 11, 2023
- 2 min read
When it comes to equipment downtime tracking, a manufacturer's number one goal will always be continuous improvement. No piece of machinery, regardless of quality, will go without the occasional issue for its entire lifespan. But as you learn more about what you're doing that isn't working, you can fix those issues to increase performance - thus getting the highest possible return out of your investment.
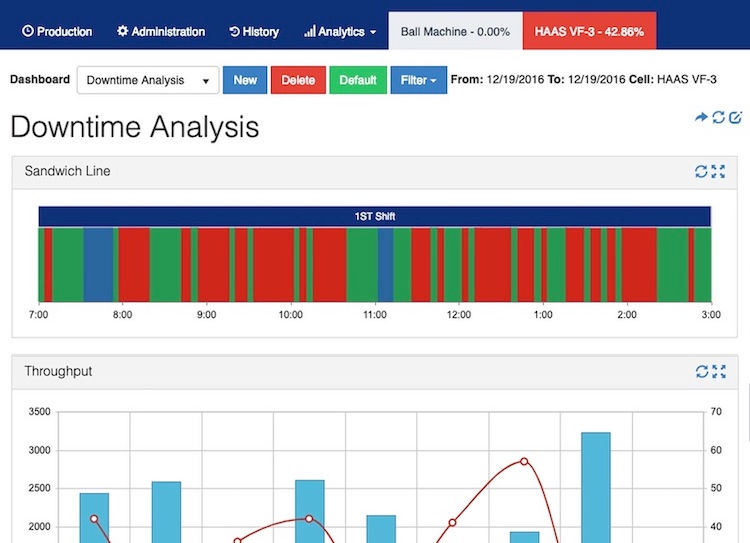
That simple idea is at the heart of many emerging trends in the manufacturing industry, with digital twins being chief among them. They've become commonplace over the last few years thanks to the rise in smart manufacturing and they offer a number of distinct benefits that cannot be ignored.
Why Digital Twins Are Becoming More Popular All the Time
At its core, a "digital twin" is essentially a virtual model of not only the machines that are in operation on your factory floor, but the processes that control them. The goal is to collect as much data as you can in order to gain greater control (and insight) into what is going on, when, where, and why.
The most immediate benefit of this is that it allows businesses to essentially test and make an argument for a product before it even technically exists. You can build an exact replica of your planned production process within the context of a digital twin, which allows you to instantly see what elements of that process would work and which ones could be improved. Then, when you're ready for the actual production part of the equation, you've identified and put an end to various mistakes and missteps before they've had a chance to cost you time and money.
Of course, digital twins offer a number of other benefits as well - particularly when it comes to predictive maintenance. Because machine downtime tracking solutions are generating data and analyzing it in real-time, problems with both processes and equipment within the system can be identified faster than ever.
For the sake of example, let's say your OEE score is dropping on a particular line and you aren't sure why. By keeping an eye on the real-time data - and by recreating the line by way of a digital trend - you can test certain hypotheses to see which efforts will have the biggest positive impact. Maybe it's a "people" issue and your workers require more training. If it's an equipment-related performance issue, you can also use the same digital twin to determine the exact right moment for preventative maintenance so that you can correct the issue without causing a major disruption.
In the end, while the technology that we use to facilitate equipment downtime tracking may change, the goals of it never will. It's all about capitalizing on any opportunity you have to work smarter, faster, and more efficiently - and it's easy to see why digital twins have become a big part of that for so many.
If you're interested in learning more about what digital twins are within the context of manufacturing, or if you have any additional questions about tracking machine downtime in general that you'd like to go over with someone in a bit more detail, please contact the team at Thrive today.
Comments